MPS connectivity & performance services are intended to unleash the full potential of the MPS machines in the world.
We provide insights about the performance of your machine(s), we connect and actively work with you to translate these insights into business improvements. This is made possible with our innovative cloud platform based on data coming directly from the machine (Internet of Things), every second of the day, 365 days a year.
Your personal virtual coach
The VirtualCoach is the newest product in the connectivity & performance service offering from MPS.
VirtualCoach is a real-time operator tool, driven by data and artificial intelligence, available on all new MPS presses. VirtualCoach gives the operator awareness on the quality and efficiency of all the activities he is performing on the press. Besides these insights it also gives real-time guidance to operate the press more efficiently. This guidance is fully personalized, based on intelligent algorithms and applied to the actual behavior of the operator. The key benefits for you as an organization:
- Bridge the gap between management wish and operator behavior
- Operator involvement in continuous improvement process
- Real-time training for operators
- Faster skill development of operators
- Continuous and personalized feedback
- Updated every 5 seconds
Features
Live analysis of the press state, quickly spot active and inactive standstill
time. The blue line represents the actual web speed.

Detects in which jobphase the job currently is and how long it took:
Durations of steps within the printing process and if they have been completed or not. For example, it allows the operator to see that the pressure settings still need to be completed and that the register settings have been completed in 2 minutes and 47 seconds.
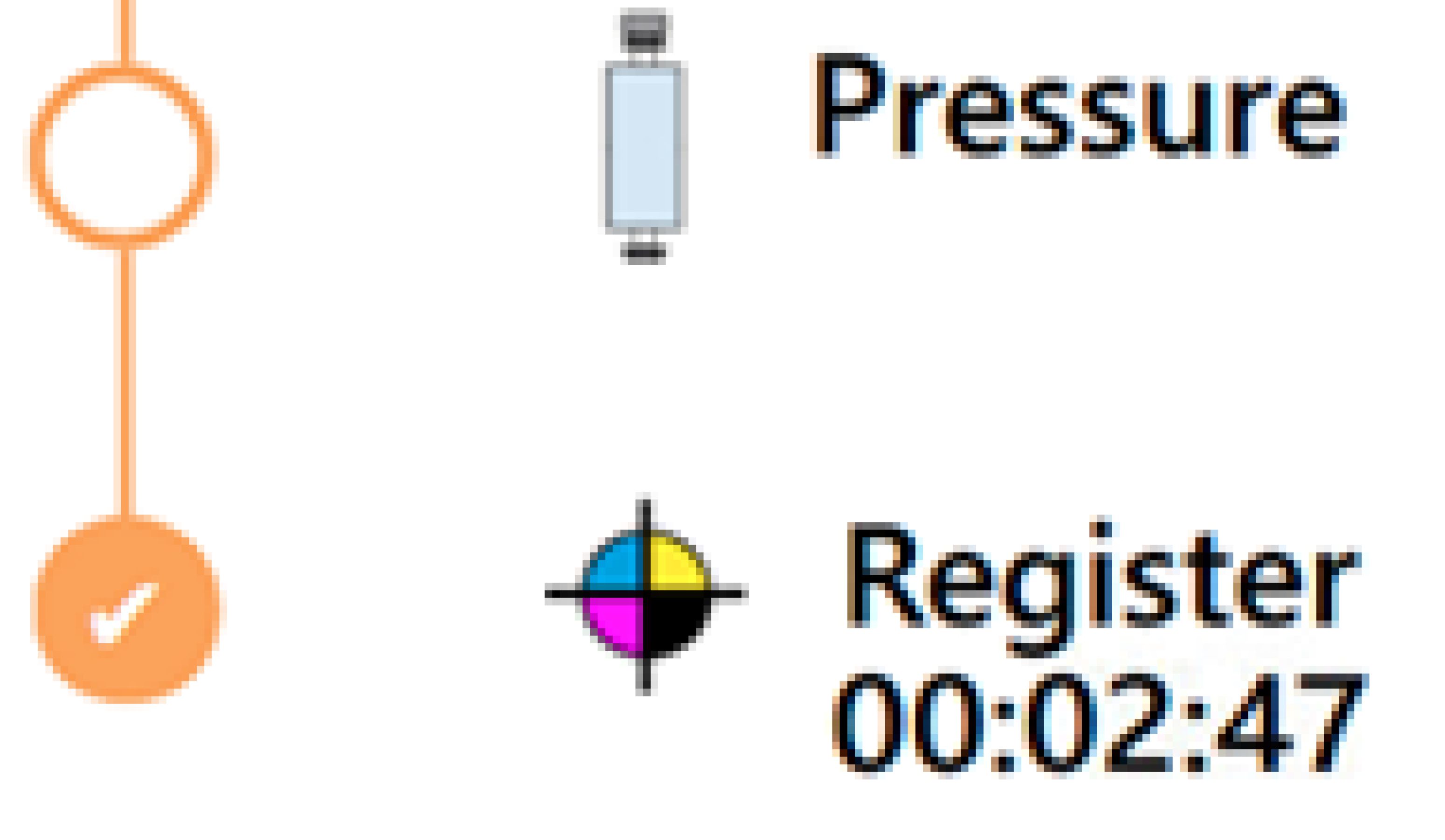
Material length consumed since the last rewind and unwind change and the number of rewinds / unwinds within the current job.
Job data such as: Job Time, Average Production Speed and Job Waste Percentage
Live feedback and tips. In this box, operators will get feedback on how they performed steps within the job. For example, how fast the sleeve change was compared to operator benchmarks and which steps could be improved in the printing process.
Do you want to know more about it?
Please contact your local agent or the performance team from MPS.